Metal Stamping: Everything You Required to Know About the Process
Opening the Power of Metal Stamping: Approaches for Boosted Item Development
In the world of manufacturing, the application of metal marking holds a considerable area because of its flexibility and performance in creating detailed parts and components. The real potential of steel marking stays untapped by several companies seeking to boost their product growth processes. By discovering advanced techniques and strategies tailored to enhance layout, product option, production efficiency, and high quality control, companies can unlock a riches of possibilities to boost their products to brand-new elevations of development and performance.
Benefits of Metal Stamping
Steel stamping offers a cost-efficient and effective method for creating premium steel components. This manufacturing process involves shaping, cutting, or creating steel sheets making use of a marking press (Metal Stamping). One of the vital advantages of steel marking is its capacity to produce complicated geometries with high accuracy and consistency. This is particularly useful for markets such as auto, aerospace, and electronics, where elaborate metal parts are typically called for.
Moreover, metal marking permits high-volume production, making it suitable for jobs that call for huge amounts of metal components. The rate and repeatability of the stamping process not just make certain expense financial savings yet additionally add to faster turnaround times for manufacturing orders. Furthermore, the use of automated tools in steel stamping assists reduce the risk of human mistake, causing improved overall item quality.

Layout Optimization Strategies
With mindful consideration of product properties and geometric setups, layout optimization techniques play an important role in improving the performance and capability of metal marking processes. By strategically assessing factors such as material strength, type, and thickness, producers can customize the layout to maximize the performance of the stamping procedure. Utilizing simulation software, engineers can forecast exactly how various design variants will certainly act under different marking problems, permitting the identification of prospective issues before production begins.
Additionally, integrating features like fillets, chamfers, and embosses into the design can improve the total top quality of the stamped component while lowering the danger of flaws such as contorting or fracturing. Furthermore, enhancing the layout of features on the component can enhance the product circulation during marking, causing more specific and constant end results.
Fundamentally, style optimization techniques enable manufacturers to adjust their steel stamping processes, causing improved product high quality, boosted manufacturing effectiveness, and eventually, a more affordable placement out there.
Product Option Methods
Style optimization techniques in steel stamping processes greatly depend on strategic product choice methods to make certain the wanted efficiency and efficiency of the made components. The choice of product in steel stamping is crucial as it directly influences the quality, longevity, and general functionality of the end product. When picking the suitable material for a specific project, elements such as mechanical residential or commercial properties, rust, cost-effectiveness, and formability resistance should be taken into account.
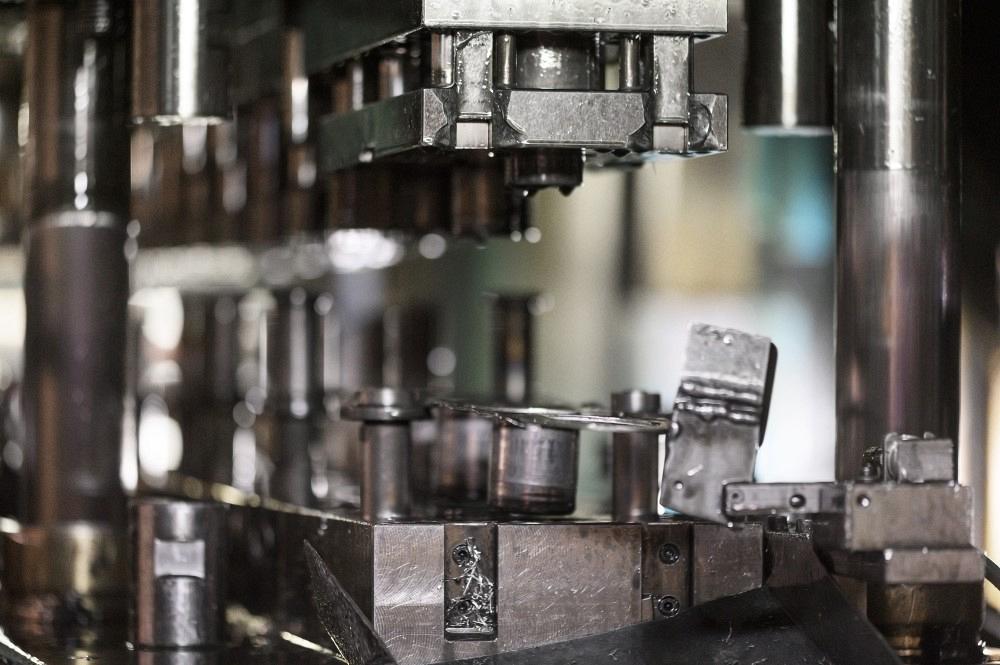
Balancing the performance requirements with the overall expense of materials is vital to guarantee the financial stability of the production procedure. By meticulously examining these aspects, makers can optimize their product selection techniques to achieve superior product quality and operational effectiveness.
Enhancing Production Efficiency
Efficiency in production processes is a crucial variable for ensuring cost-effectiveness and prompt delivery of top notch metal stamped components. To improve manufacturing performance in steel stamping, several methods can be implemented.
Furthermore, check over here applying automation and robotics in metal stamping procedures can considerably raise performance and uniformity while reducing labor costs. Automated systems can carry out repeated tasks with high precision and rate, bring about improved browse around these guys manufacturing effectiveness and higher outcome rates. Buying modern stamping devices with sophisticated attributes, such as servo-driven presses and quick die modification systems, can further optimize production procedures and reduce downtime.
Furthermore, developing clear communication networks and cultivating partnership between engineering, manufacturing, and layout groups is critical for determining potential traffic jams and executing continuous enhancements in the manufacturing operations - Metal Stamping. By embracing lean manufacturing concepts and leveraging technology improvements, manufacturers can open the complete possibility of metal marking processes and accomplish better manufacturing efficiency
Quality Assurance and Evaluation Techniques
To ensure the constant manufacturing of high-quality metal marked parts, extensive quality assurance and inspection techniques play a pivotal role in verifying the accuracy and integrity of the production process. Quality assurance in metal stamping involves a series of methodical checks and measures to guarantee that each component satisfies the given requirements. Inspection methods such as visual evaluation, dimensional analysis, and product screening are frequently utilized to examine the high quality of stamped parts. Visual inspections guarantee the surface finish and stability of the parts, while dimensional evaluation verifies that the parts adapt the called for specs. Material screening strategies like solidity screening and product composition analysis assistance verify the material buildings and architectural stability of the stamped components. Additionally, progressed innovations such as automated optical assessment official source systems and coordinate determining machines are significantly being utilized to boost the accuracy and efficiency of quality control processes in steel marking. By carrying out robust quality assurance and examination approaches, manufacturers can support high requirements of quality and consistency in their metal stamped products.
Verdict
In final thought, metal stamping deals countless benefits such as cost-effectiveness, precision, and versatility in item growth. On the whole, opening the power of steel marking needs a calculated method to enhance product development processes.
Metal marking offers a reliable and economical technique for producing premium metal components.Additionally, metal marking enables for high-volume production, making it optimal for jobs that need large amounts of metal parts.Via careful consideration of product buildings and geometric setups, style optimization techniques play a vital function in enhancing the performance and performance of metal marking processes.Layout optimization techniques in metal marking processes heavily count on tactical product choice methods to ensure the preferred efficiency and effectiveness of the made parts. The selection of material in metal stamping is vital as it straight affects the high quality, sturdiness, and overall functionality of the final item.